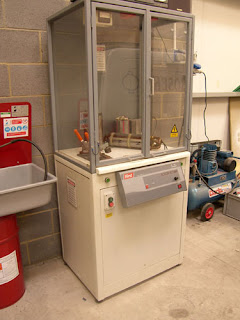
Field service and maintenance specialist CP Automation has announced a service and repair technique for DC drives, attached to permanent magnet motors, that is set to make in-house re-setting of the serviced drive a thing of the past. The technique dispenses with the use of a ‘keeper’, which normally acts as a substitute for the armature in the servicing procedure. Instead, the company de-magnetises the motor before repair and then re-magnetises it afterwards to the correct setting.
The company utilises a set of specialist tools, including a magnetising cabinet, as well as intellectual property built up over decades in the drives industry to apply the new technique.
The reason that the settings on DC drives attached to motors that have been serviced or re-wound in their lifetime are often incorrect is that there is something unique to be borne in mind when repairing or servicing a DC permanent magnet motor. The standard philosophy within the rewind industry is to remove the armature and replace it with a ‘keeper’; to stop the levels of the magnets degrading. However, older magnets, and the material used to manufacture some newer magnets, will degrade while the armature is being removed and the keeper is being put in its place. The same applies when the armature is put back in after repair or service. The result is increased RPM and lost torque, which may mean the motor draws more current, costing money and creating a greater environmental impact.
If the CPA process isn’t used, an in-house engineer has to re-set the DC drive to cope with the changes to the motor. As a result, all the systems in the plant eventually become unique and cease to be interchangeable. The only solution is to de-magnetise the motor before repairing it and then re-magnetise it to the correct level afterwards, as CP Automation does. The company derives the calculation for this from the speed and EMF (Electro Motive Force) settings on the name plate of the motor.
“Plant managers want to swap equipment around in the event of a breakdown or maintenance issue,” explained Tony Young, a director of CP Automation. “However, they often find that the DC drives attached to permanent magnet motors on different production lines have different settings – making it hard to interchange things easily. Our solution means that that the settings will be exactly as specified on the name plate, meaning they can be swapped around easily.”
Ends: 413 words
Editor’s note: If you want to stay constantly up to date on the latest news from CP Automation, paste the following link into your RSS reader http://cpa-pr.blogspot.com/atom.xml. If you don’t have an RSS reader, I can recommend the following free package Sharp Reader.
For further information contact:
Tony Young, CP Automation
Unit 8, Ashley Industrial Estate, Exmoor Avenue,
Scunthorpe, DN15 8NJ
Telephone: +44 (0)1724 851 515
Fax: +44 (0)1724 851516
www: http://www.cpaltd.net/ and http://www.euroserveltd.net/
e-mail: tony.young@cpaltd.net
Press enquiries: Richard Stone
Stone Junction, 33 Kirkdale,
Sydenham, London, SE26 4BT
Telephone: +44 (0) 20 8699 7743
Fax: +44 (0) 20 8699 7743
e-mail: richards@stonejunction.co.uk
www: http://www.stonejunction.co.uk/
About CP Automation: CP Automation is a specialist in the repair and replacement of automation equipment including electronic boards, PLCs and Ac and DC drives. It was established to provide an independent maintenance service, without exclusive ties to any manufacturer. However, it does have strong relationships with the principal inverter, encoder, resistors and motor manufacturers.
Ref: CPA011/01/08